D.A.T.E.
TECHNICAL SOLUTIONS
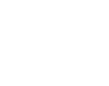
Manufacturing Capabilities
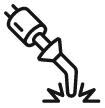
Electrical and TIG Welding
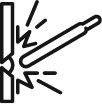
Brazing
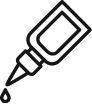
Gluing
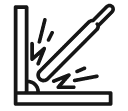
Assembly
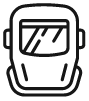
Metalwork
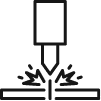
Laser and mechanical cutting et Laser

Pressure and leak tests and tightness

Experimentalqualification : Aeraulic and hydraulic bench tests
Manufacturing
Raw Material | Stainless steel | Stainless steel (inconel 625) | Aluminum | Copper |
---|---|---|---|---|
Welding | TIG with filler metal | TIG without filler metal | Spot welding | Semi-automatic welding |
Brazing | Copper on copper (Sn or Ag) | Stainless steel on copper (Ag) | Aluminum on Aluminum (vacuum brazing)
| |
Gluing | Structural | Epoxy single component | With or without thermal load | |
Metalwork | Stamping | Punching | Laser Cutting | Folding |
Drilling | Tapping | Rolling | Bending | |
Plate fins Manufacuring (homemade Machine) | ||||
Assemby | ||||
Wiring |
Controls and testing
Tightness | ||||
---|---|---|---|---|
Dimensional | 3D | Manual | ||
Assemby | ||||
Thermal performance | Air / Air | Air / Water | Water / Water
| Thermal Chamber (-70°C,+150°C) (-94°F,+302°F) |
Pressure drop | ||||
Electrical | Mass continuity | Isolation | Dielectric rigidity |
Design and calculation
Thermal and Fluid calculation | SolidWorks | Fluent | DATE internal software (special abilities) | |
---|---|---|---|---|
Mechanical calculation | Ansys | |||
Design | Solidworks |
Heat pipe scheme
Heat pipes are essential components for providing effective thermal management in various industrial systems.
A heat pipe is a closed tube which contains a fluid (often a liquid with a low boiling temperature) circulating between its two ends depending on temperature differences. They make it possible to maintain a uniform temperature, thus meeting the requirements of the most complex applications.
We mainly deal with three types of heat pipes, each designed for specific uses:
- Melt lines: Ideal for plastic transfer.
- Cylinders: Used for various applications, such as the production of plastic films.
- Bells -: These heat pipes use stainless steel screen technology, ensuring even heat distribution and protection against temperature variations.
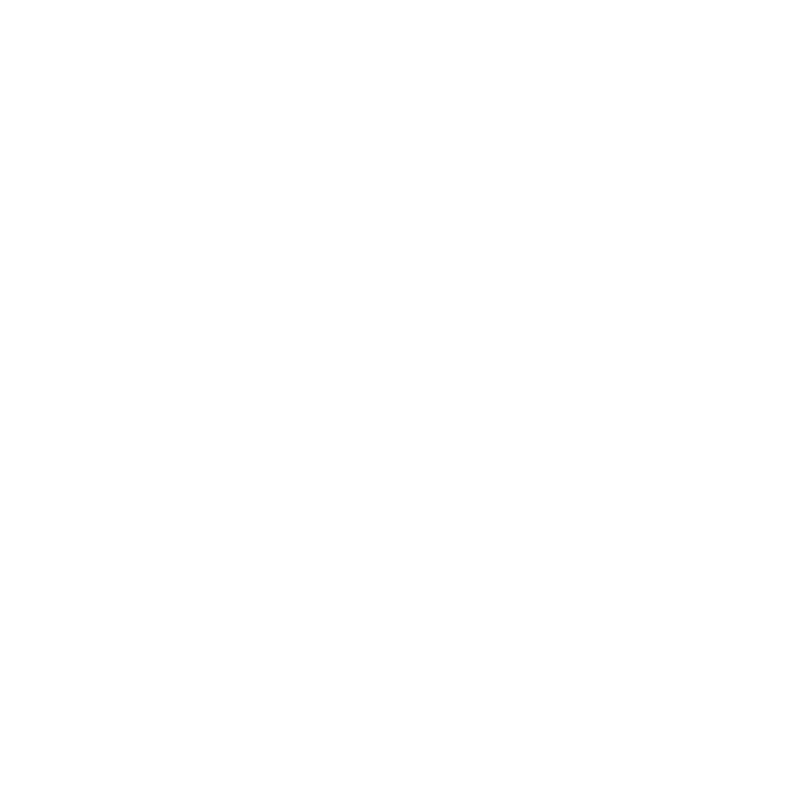
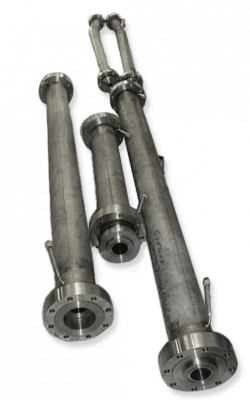
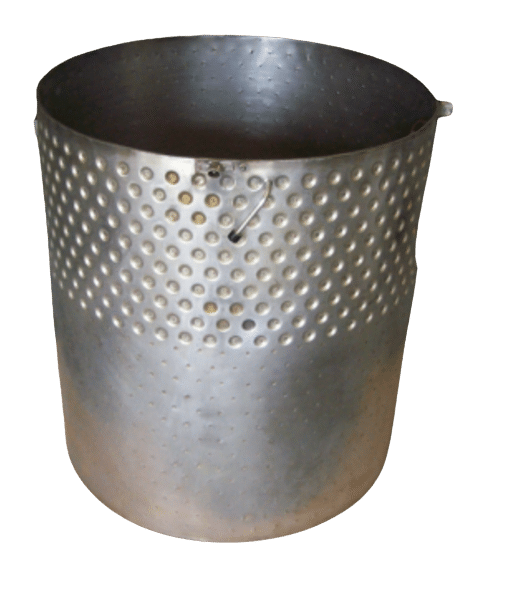
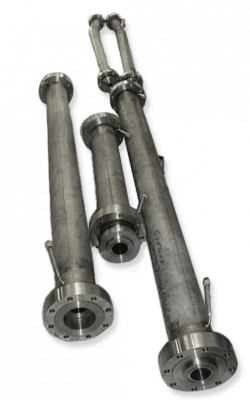
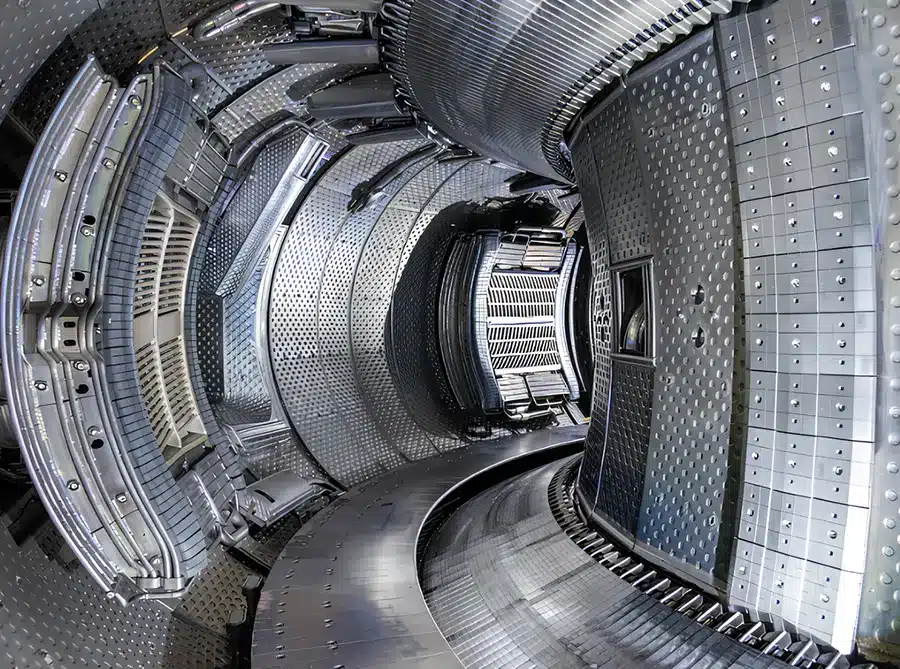
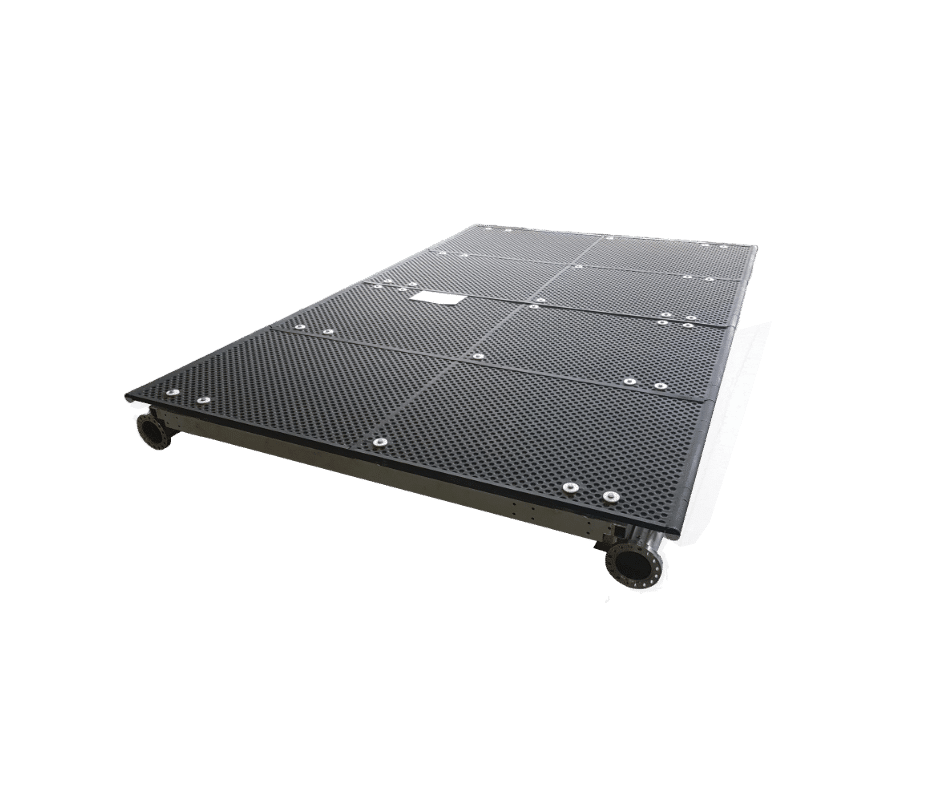
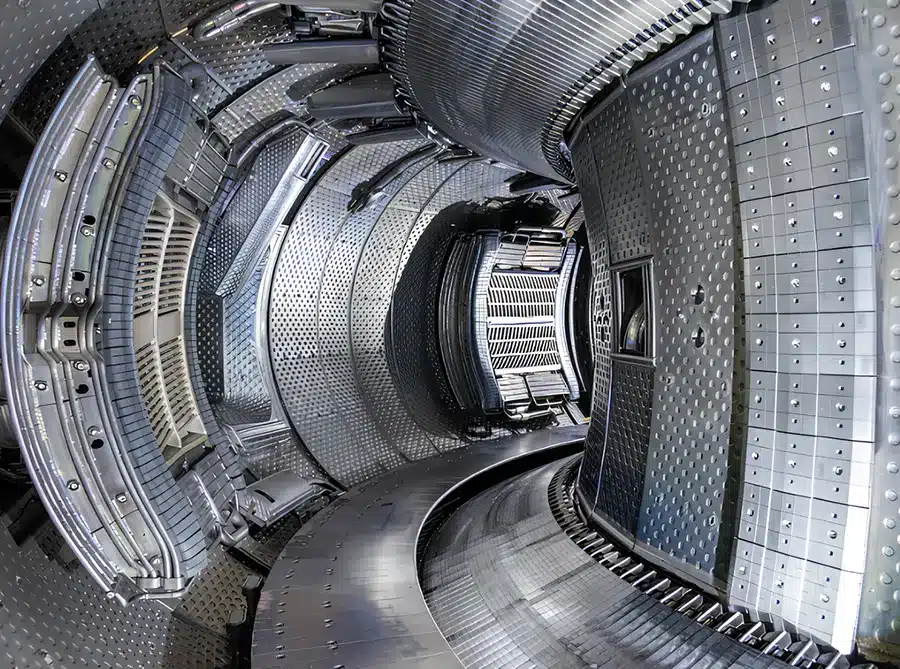
Thermal shrouds
We use various quality materials and techniques to guarantee the performance and durability of our thermal shrouds:
- Stainless steel 304L, 316L 316 Ti… These stainless steels offer excellent resistance to corrosion and heat.
- Nickel alloys Used for spot-welded screens, these alloys are renowned for their strength and resistance to extreme temperatures.
- Copper for screens with brazing Possibility of creating stainless steel accessories for specific applications.
We specialize in point-welded stamped screens, also using other types of welding such as TIG. Our stainless steelthermal shrouds, comprising spot welded elements and tubes brazed to sheets, are versatile protection systems. They are used to protect equipment exposed to extreme conditions, such as the multi-million degree plasma flow in the Tore Supra. They are also suitable for simulating environments in sectors such as space. These screens are also used in our air/water exchangers and in our heat pipe activities, using advanced welding technologies.
Temperatures | From 80K to 500K |
---|---|
Dimensions | On request |
Uses | Space, science & research… |
Main fluids used | Liquid or gaseous nitrogen, water, brine |
Cold plates
Cold plates are essential for efficiently transferring heat from components, usually electrical, to a cooling circuit.
We offer several technologies to meet the diverse needs of our customers:
- Vacuum brazed technology
- Copper brazing technology
- Bonded Technology – Features TIG-welded stainless steel coils embedded in an aluminum plate with thermal glue.
Temperatures | 20° to 100° |
---|---|
Dimension | Made to measure |
Uses | Industry, aeronautics, defense… |
Main fluids used | Water or brine, heat transfer fluids |
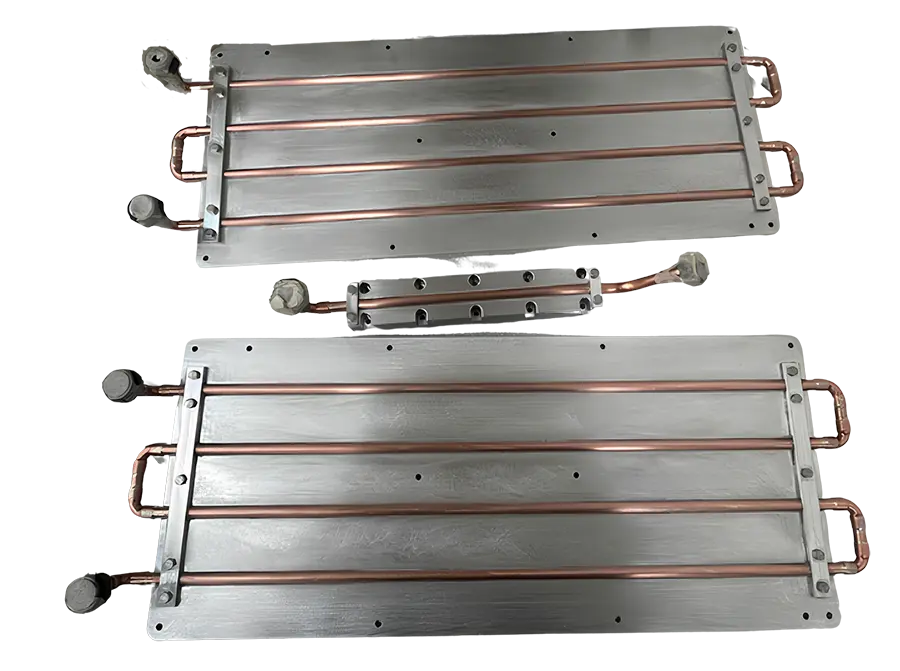
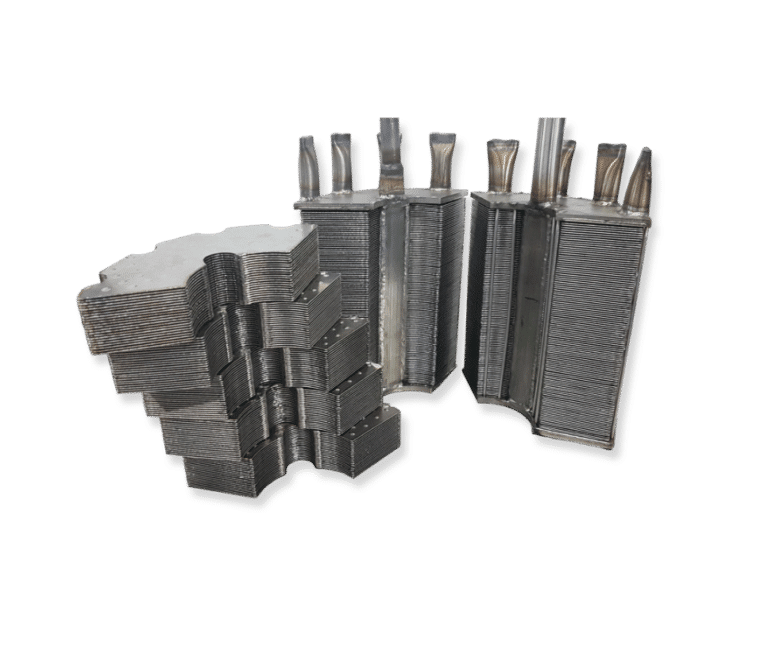
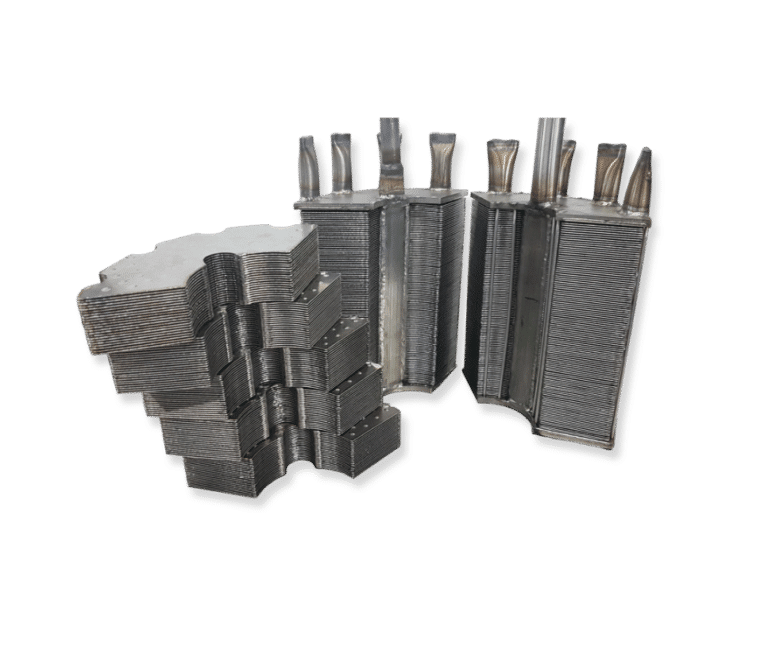
Plate exchangers
Our plate heat exchangers are designed to efficiently transfer thermal power between two or more fluids, with or without phase changes.
These exchangers use materials such as stainless steel or nickel alloys. The assembly method is done only with TIG welds.
Temperatures | 1,5K to 1000K |
---|---|
Dimension | Made to measure |
Uses | Defense, particle gas pedals, hydrogen, industry… |
Main fluids used | He, H2, O2, N2, H2O, CH4, Xe… |
Screen-fin exchangers
Our screen-fin heat exchangers are designed to efficiently transfer thermal power between a gas and a fluid.
These exchangers are particularly suitable for cooling systems, such as air cooling with water for electrical cabinets, for example.
- Stamped Plates and Crushed Tubes – For the fluid circuit, we use stamped plates or crushed stainless steel tubes, ensuring excellent heat transfer. Stamped plates are preferred due to their better thermal performance.
- Bonded Aluminum Fins For the gas circuit, the fins are made of 1050 aluminum and bonded with thermal glue, thus improving heat transfer between the plates and the fins.
Temperatures | -40° to 100° |
---|---|
Dimension | Made to measure |
Uses | Defense, research and science, industry… |
Main fluids used | Water, brine, heat transfer fluids |
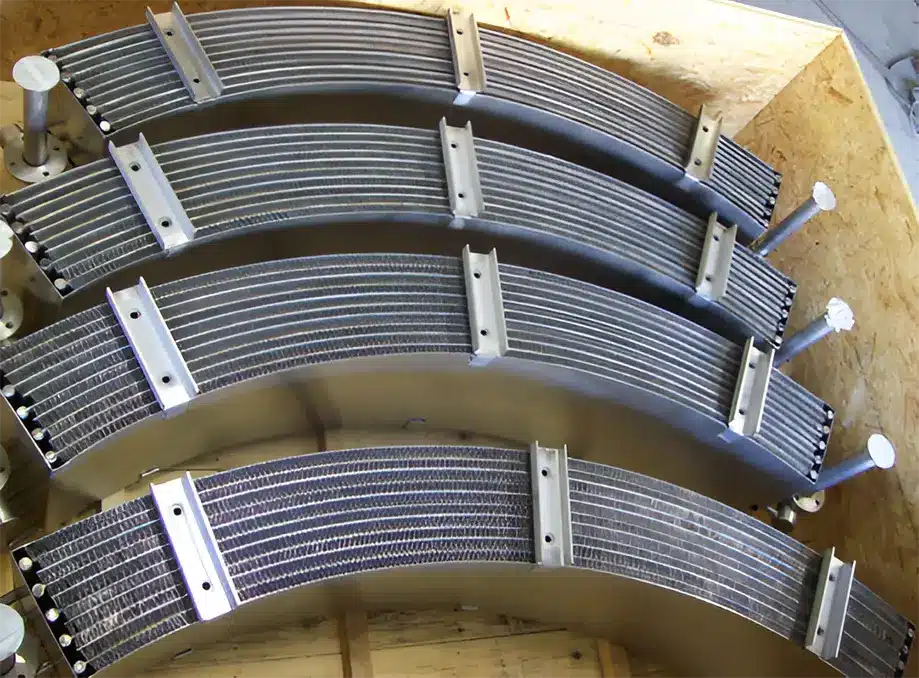
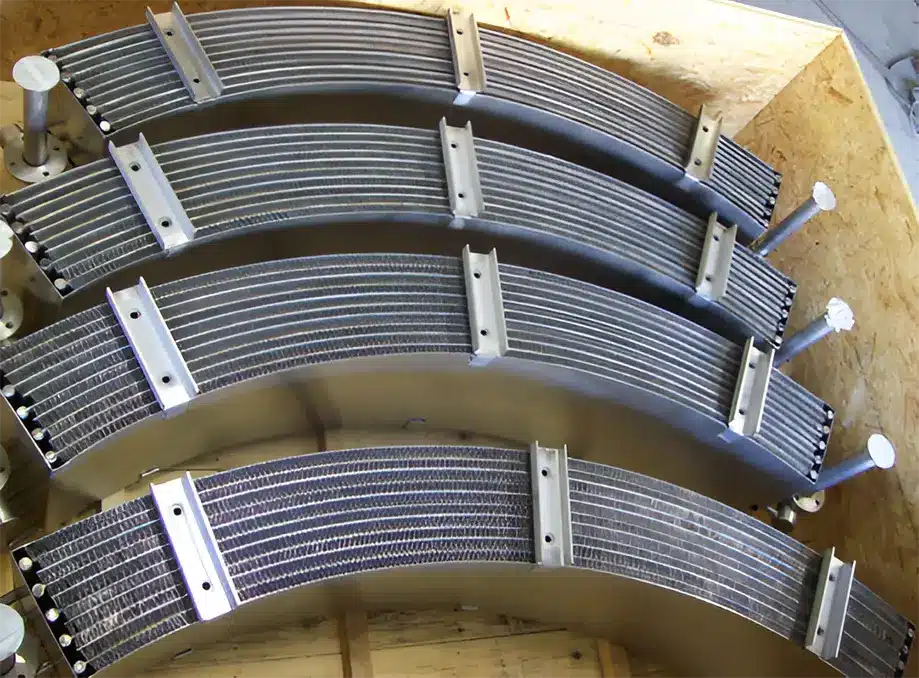


Fin-fin exchangers
Our fin-to-fin heat exchangers operate efficiently over a wide temperature range and are suitable for various industrial uses. They are ideal for gas-to-gas applications.
Materials Aluminum: Used for the fins, this material ensures excellent thermal transfer and increased durability.
Thermal Adhesive: Used in bonded technology to improve heat transfer between fins.
Bonded Technology – The exchangers use 1050 aluminum fins, bonded with thermal glue to improve heat transfer.
Vacuum Brazed Technology – This method is mainly used if the temperature is below 100°C.
Temperatures | -40° to 100° |
---|---|
Dimension | Made-to-measure |
Uses | Defense, industry… |